Fuel Polishing vs Tank Cleaning: what does your backup power need and does it really work?
Published Tuesday 3 September, 2019
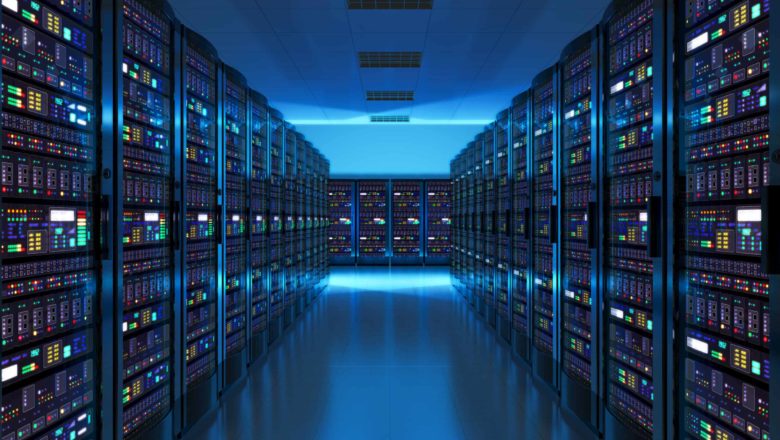
Modern refining techniques have reduced the shelf life of diesel fuel, and the legislative changes that lead to the introduction of bio has only compounded the issue of fuel degradation and contamination. This has resulted in increased demand from businesses looking for products and services such as fuel polishing and tank cleaning to help tackle and resolve fuel contamination. However, it’s essential to understand the difference between the services to ensure you manage your fuel contamination in the most effective way.
What is fuel polishing and does it work?
The term ‘fuel polishing’ is used to describe the practice of filtering contaminated fuel through several stages to remove water, sediment and microbial contamination. Following this process, any lost additive properties are restored, the fuel is tested and additional enzymes are then often combined with the fuel. These enzymes are designed to advance the quality of the fuel by blending in cetane, improving lubricity and ensuring fuel stability. When the polishing process has been completed your fuel should be restored back to industry specifications. So does this mean your fuel contamination issues are no more? Unfortunately, no, and there are two main reasons why:
Firstly, when fuel has become contaminated it’s likely to become contaminated again as the fuel’s stability has been affected by the contaminates. So, its highly recommended that businesses ensure they adopt a fuel management policy which includes the frequent sampling of fuel from multiple levels within the oil tank to manage and treat any further contamination as quickly as possible.
Secondly, fuel polishing is only likely to have resolved your contamination issues if the newly polished fuel is going to be pumped back into a contaminate free fuel tank, so either a tank that is brand new or one that has not been affected by the contaminates.
This is because fuel polishing will only restore the fuel itself, so the process can be unproductive when it comes to dealing with a tank that stored highly contaminated fuel. The tank’s exposure to contaminated fuel will have resulted in microbial growth lining the tank. So, when the newly polished fuel is pumped back into the tank, the microbial growth on the tank walls and struts will quickly re-contaminate the fuel, putting you back to square one in a very short amount of time.
Therefore, the method of fuel polishing alone could be ineffective if in fact you require more than just fuel polishing to remedy your fuel contamination. The need for additional contamination services can be particularly true for businesses reliant on fuel for backup power such as facilities management companies and data centres.
If fuel polishing isn’t going to do the job, what is tank cleaning and does it work?
Tank cleaning involves the fuel and the contaminated contents to be drained from the tank, the inside of the tank will then be cleaned and disinfected. The process of tank cleaning is often completed using industrial vacuums to manually remove microbial growth, sludge and heavy sediment build-up that collects at the bottom of the tank, on the tank walls and struts. When the inside of the tank has been cleaned, the tank will then be disinfected. While some companies still use Biocides as opposed to modern alternatives, such as Soltron, these modern disinfectants are considered by some to be a more effective and environmentally friendly alternative to traditional Biocides.
The fuel that was removed from the tank can then be polished (as above) and pumped back into the clean tank or the contaminated fuel can be disposed of and replaced with fresh fuel. Replacing the contaminated fuel with new fuel is the most effective way to eliminate any contamination issues and ensure optimum resilience but this does impose a significantly higher cost when compared with the costs of fuel polishing.
The option of fuel replacement is often favoured by businesses that rely on fuel for backup power as stagnant fuel increases the risk of fuel contamination considerably. It’s also worth noting that those businesses that rely on fuel for resilience should consider selecting a company that offers a temporary backup tank whilst works are completed to prevent any exposure to downtime – this isn’t something every company offers as standard.
So, how to you know what service you need?
Before you proceed with either fuel polishing or tank cleaning it is essential that you have your fuel sampled. This will help ensure you’re not paying for something that may not be required. There are varying types and degrees of contamination so the correct diagnosis though effective sampling is essential. Samples should be collected from multiple levels in the tank.
As previously mentioned, contaminates are heavier than the fuel itself so the first sample should be taken from the bottom of the tank and this should start to provide an insight into how the following samples are likely to be received. If your first sample clearly displays dissolved, emulsified or free water, your following samples are likely to display further evidence of contamination. The general rule is that the higher up the collection points of samples are within the tank that still display evidence of contamination, the more likely you are to need tank cleaning and fuel polishing. If the samples are displaying moderate levels of contamination, it’s likely that fuel polishing will be your answer. However, if you can clearly see evidence of corrosion on the tank, such as rusting, it’s likely that the microbial growth has started to eat away at the tank walls leaving the tank unfit for purpose.
Still not sure what you need?
We work daily with some of the UK’s largest blue chip companies, in addition to critical facilities, data centres and facilities management companies. With numerous preventative and reactive measures that can be adopted to ensure fuel quality and resilience, we work to ensure the right services and products are selected for each of our clients, bespoke to their current fuel situation and future business needs.