The science behind facility resilience: why filtration systems are critical
Published Tuesday 3 September, 2019
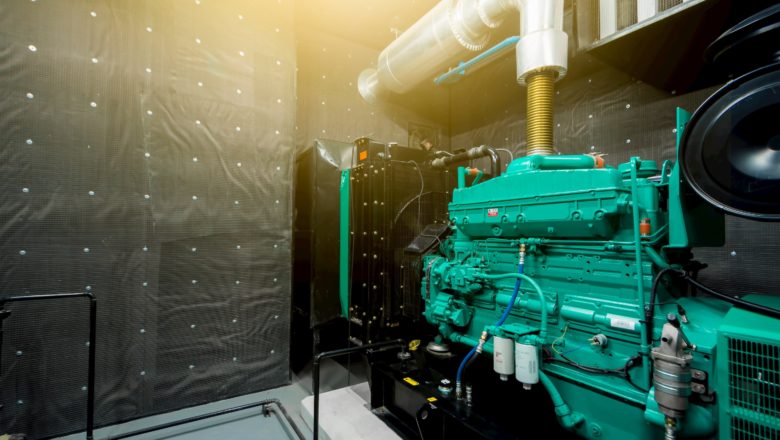
It seems each week sees a new headline about the cost – in time, money and reputation – that a critical facility endures when they fall victim to a power outage. Often when these power outages are investigated further, it’s highlighted that this downtime is a result of contaminated fuel, something which could have easily been prevented.
Reliance on fuel is often a last resort when a critical facility, such as a data centre, experiences a power outage. Critical facilities often have multiple automatic triggers that take place when the dominant power supply becomes compromised. However, when the final component in the chain of reactions has been reached, a back-up diesel generator should kick into action to provide the necessary power.
These diesel generators should power up within seconds to produce a seamless supply of power to the facility. Unfortunately, the ultra-fine tolerances of today’s super-efficient diesel generator engines mean they are extremely sensitive to any fuel quality problems or fuel contamination. This can mean that when the fuel is contaminated, the performance and resilience of the generator can be seriously compromised resulting in downtime and power outages.
So, how does fuel become contaminated and why are critical facilities at an increased risk?
Fuel can become contaminated in a number of ways; through simple human error, poor refuelling practices or various unpredictable external sources. However, within the critical facility industry the main cause of fuel contamination is due to fuel being stored for long periods of time.
Stored fuel is at risk of becoming stagnant, making it susceptible to natural degradation and water contamination. The combination of which is greatly damaging to both the fuel quality and resilience. Unless this is identified, it will quickly render the fuel unfit for purpose.
Water contamination is the most common component due to the natural condensation that occurs within fuel tanks and the atmospheric absorption qualities of fuel. When water enters the fuel, microbial growth will begin to form and is heavily accelerated when you couple higher FAME (Fatty Acid Methyl Ester) content with lower Sulphur content.
Until recent changes in diesel specification, this was something that critical facilities didn’t have to consider. Although Sulphur once provided increased protection against microbial growth, recent regulations now impose a lower Sulphur content in fuels which, although beneficial for the environment, reduce the fuel’s stability and reliance.
If microbial growth is left untreated, aerobic and anaerobic bacteria will feed on the hydrocarbons in the fuel and nutrients within the water. With the reduced hydrocarbons, the combustion process of fuel becomes increasingly difficult and damaging for generators.
So, with the combination of water-induced contaminates and reduced combustion, how will a flirtation system ensure resilience?
Filtration systems work to prevent fuel contamination by circulating the stored fuel and removing sediment from the bottom of the tank. Without a filtration system, contaminated fuel can often go unnoticed, threatening the uninterrupted power requirements of the facility.
However, it’s not as simple as installing the first filtration system that you come across and closing the doors to fuel contamination. We’ve seen first-hand how traditional filtration systems can be inefficient as some only reach an average of 5% of the potentially contaminated fuel. Without the capability of circulating 100% of the fuel from within the tank, pockets of fuel will become stagnant and the process of contamination will begin against your best efforts.
The best types of filtration systems will also provide real time analysis of the fuel that is being pumped through the filtration unit. This analysis will alert facilities to the first signs of contamination or water content to ensure immediate reaction, preventing costly fuel degradation.
Ensuring your facility has a filtration system that circulates 100% of the fuel within your tank whilst providing real time analysis on fuel condition is the only way to guarantee your fuel won’t let you down in the case of a power failure. The right specification of filtration system enables critical facilities to maintain fuel quality is and, more importantly, ensure your generator will power up when you need it most.
For advice on filtration systems, or if you would like to speak to one of our experts about your critical facilities fuel management, book a free consultation today. You can call us on 0800 985 6172 or email at sales@thewp-group.co.uk.